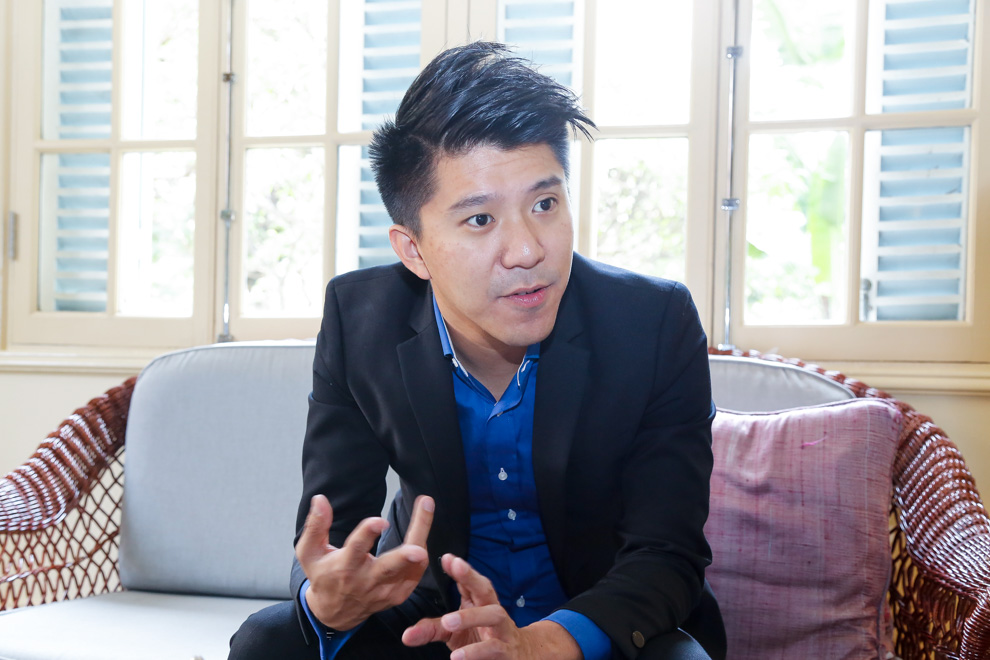
Kelvin Chua, the sales and marketing director for Le Urban Eco Park, talks to the Post last week in Phnom Penh.
A new industrial park on National Road 3 is vying to attract investment with its eco-friendly building standards and incorporated residential and commercial areas, with a goal of becoming a hub for energy-conscious and cost-sensitive investors. The Post’s Kali Kotoski spoke with Kelvin Chua, sales and marketing director for Le Urban Eco Park, about what makes this industrial park different.
How have you incorporated green or eco-friendly construction into the industrial park?
For the factories portion of our industrial park, we actually got the strict Singaporean Building and Construction Authority (BCA) to approve our buildings with Green Mark certification. What we try to do in our construction is to use reliable materials like concrete instead of bricks and recycled steel. But more importantly, we have very energy-efficient buildings. Right now, most existing factories are very blocked up and that causes issues of not having natural lighting or ventilation, making them use a lot of electricity on air conditioning or water cooler fans.
How are your tenants saving money by using your buildings?
One of our tenants, who actually had an existing 7,000 square metre garment factory in Stung Meanchey and moved to us and almost doubled the size of their factory, is already seeing the electricity cost dropping from $20,000 to $10,000 per month. Basically, our factories have a lot of glass and open ventilation. This creates a natural cooling and bright environment so factories do not need to use any electricity for lights during the day.
How does BCA approval help marketing the industrial park?
Well, because Cambodia lacks any building regulations, we wanted to be the first eco park, so we needed this certification. We were not always confident about how much the cost savings would be once we were operational, but now that we have a garment factory that is at 100-percent capacity and saving half the amount on electricity, we have the numbers to back it up.
How important is the use of solar power?
We try to use a bit of solar, but only on a limited scale at the moment. We would like to use more solar, but there are still concerns with how reliable the batteries are. And of course, solar investment is not cheap. I would say we are already 80 percent self-reliant and eco, but not all the way there. But to be 100 percent self-reliant by using solar is rather ambitious. Factories can’t afford to stop production because of issues with solar batteries, so as much as we want to be fully energy self sufficient, our responsibility is with our tenants.
How much have you invested into the industrial park?
To date, we have spent about $25 million and the projected costs to be fully operational are around $50 million. But we are already planning about a 12 to 15 percent return on investment from our current selling numbers and the rising cost of land along National Road 3. To be honest, we spent a lot more than we expected to. We have 25 hectares with 20 hectares dedicated for factories that can either be rented out or sold. But if a company buys into our park to build a factory, they will have to follow our specifications.
Do you see Cambodia as having a lot of potential to attract investors into industrial parks?
We have been talking to a lot of companies from different countries that all have factories in China. And they are all looking to move, and have to move, because labour costs there are too high. They are just not sure which country in the region to go to. But of course, it takes time for companies to do their feasibility studies and see if Cambodia is the right destination. We are competing in the region for investment, but Cambodia has its advantage of being able to import materials without much tax.
This interview has been edited for length and clarity.
Contact PhnomPenh Post for full article
SR Digital Media Co., Ltd.'#41, Street 228, Sangkat Boeung Raing, Khan Daun Penh, Phnom Penh, Cambodia
Tel: +855 92 555 741
Email: [email protected]
Copyright © All rights reserved, The Phnom Penh Post