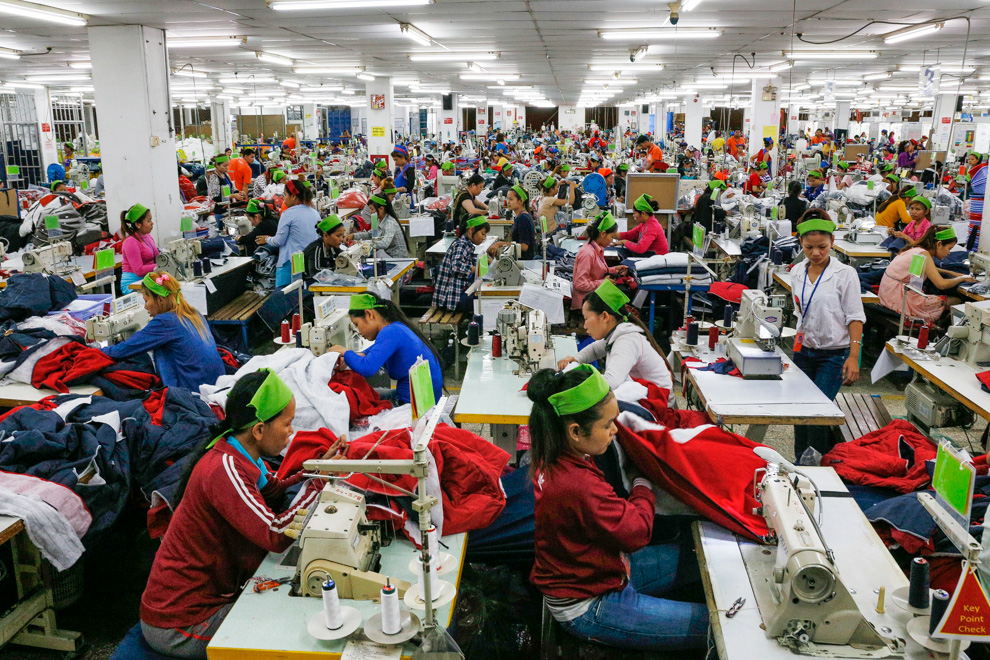
Garment employees work on the factory floor to produce items of apparel in Phnom Penh’s Por Sen Chey district in 2014.
Local industry experts responded yesterday to a new report that warns the majority of Cambodia’s garment sector workers could lose their jobs in the coming two decades as automation and innovative technologies replace low-skilled labour and allow multinational producers to move their operations closer to market.
A study by the International Labour Organization (ILO) released on Thursday found that 88 per cent of Cambodia’s salaried textile, clothing and footwear (TCF) workers were at high risk of automation. It outlined a number of technologies that stand to disrupt the sector, including 3D printing, body-scanning technology, computer-aided design (CAD), wearable technology, nanotechnology, environmentally friendly manufacturing techniques, and robotic automation.
Chief among the automation threats, according to the ILO report, is the growing prevalence of automated cutting machines and the expected rise of robots capable of sewing known as “sewbots”. While sewbots are unlikely to displace current workers in ASEAN garment factories, they are expected to be deployed in destination markets such China, Europe and the United States.
This is particularly bad news for countries like Cambodia, which rely heavily on the garment sector to provide employment for large numbers of low-skilled workers.
“For some countries like Cambodia, where TCF production dominates an undiversified manufacturing sector and makes up around 60 per cent of manufacturing employment, the impact will be felt more strongly than others,” the report said.
Kaing Monika, deputy secretary-general of the Garment Manufacturers Association in Cambodia (GMAC), said that while it is a general trend that investors equip their factories with cutting-edge technologies, this is unlikely to have a significant impact on the labour-intensive nature of Cambodia’s garment industry.
“I think the new technology will help to replace manual work to some extent, but not entirely,” he said. “It cannot fully replace the work of people and there are still many roles that require people.”
He said the Kingdom’s garment industry, which was built on the back of cheap labour, would remain cost-competitive and attractive to investors if the government cultivates a good investment climate and pursues deeper market access.
“If our investment environment remains good and we can negotiate free trade agreements with major countries, our garment industry will continue to be a source of jobs,” he said.
However, Kevin Tang, general manager of All Wintex Garment Manufacturing Corp Ltd, said it was inevitable that as technology develops, industry becomes less dependent on human labour. While he said his Chinese-owned clothing company, which employs roughly 500 workers at its factory in the capital’s Stung Meanchey district, had no plan to automate, this was largely due to the limitations of technology.
“Right now the machines are not quite good enough [to justify automation] and the machinery is currently very expensive,” he said. “However, if salaries keep rising, it will become preferable to use machines instead [of manual labour.]”
He added that one advantage of full automation to factory owners is that machines cannot go on strike.
An administrator at Best Sources (Cambodia) Factory Ltd who only gave his name as Kosal said the threat of labour unrest is one factor pushing garment factory owners to invest in machinery that reduces their dependence on human labour.
“In sewing section, I don’t think technology can replace human work, but in other sections such as packaging, fabric cutting or design printing, these tasks can be handled by machinery instead of humans,” he said.
Kong Atith, vice president of the Coalition of Cambodian Apparel Workers Democratic Union (C.CAWDU), said the ILO report highlights the spectre that hangs over not only Cambodia’s factory workforce, but those of other countries as well.
“The figures in the report show how dire the threat is workers,” Atith said. “If factory owners use machines to replace workers . . . and the government does not take timely action to control it, then this [automation] will create a lot of social issues.”
Mey Kalyan, senior advisor to the Supreme National Economic Council, said technology was an unstoppable force, so Cambodia would be better off upgrading the skills and productivity of its workforce.
“We cannot avoid the evolution of technology, so we have to be ready and improve the skills [of workers] so that they are flexible to the demands of industry,” he said. “Cambodia’s workforce is still young and we have time if we start now to adjust the education and vocational system to get the desired outcome.”
Contact PhnomPenh Post for full article
SR Digital Media Co., Ltd.'#41, Street 228, Sangkat Boeung Raing, Khan Daun Penh, Phnom Penh, Cambodia
Tel: +855 92 555 741
Email: webmasterpppost@gmail.com
Copyright © All rights reserved, The Phnom Penh Post