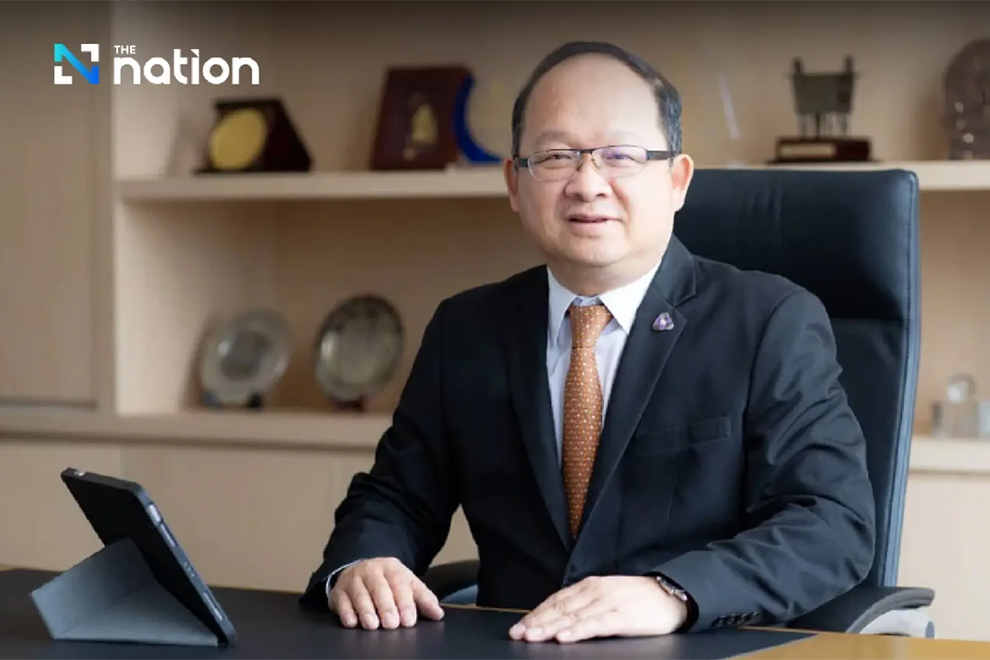
Kriengkrai Thiennukul, president of the Federation of Thai Industries (FTI). The Nation
Thailand’s manufacturing sector is facing a serious crisis with a total of 488 factories closing down in the first five months of this year, according to data with the Department of Industrial Works and KKP Research.
The average closures at over 97 a month compare unfavourably with the average of 57 factories that shut down each month in 2021.
The department data showed that from January 2022 to March 2023, a total of 1,704 factories ceased operations in the aftermath of Covid, an average of 113 closures a month.
Overall, from 2021 to May 2024, it is estimated that more than 3,500 factories have shut down.
The majority of these closures are in sectors making plastic products, leather products, rubber and rubber products, food, machinery and mechanical products, metal products, wood processing, and wood products.
Experts believe more Thai factories are likely to close down in the near future.
Kriengkrai Thiennukul, president of the Federation of Thai Industries (FTI), attributed several key factors to the trend of industrial factory closures.
He said that domestic manufacturers faced fierce competition from low-priced imported goods, especially from China, which have flooded the market through both legal and illegal channels, undercutting Thai products. This influx has affected both the retail and online markets.
Currently, China is dealing with massive liquidity issues in its real estate sector, which accounts for nearly 30% of the country’s GDP, forcing the country to increasingly rely on exports to sustain its economy.
As a result, China has ramped up production for export to compensate for the loss in GDP from the real estate sector.
"Recently, the US announced tariffs of 25-100% on hundreds of Chinese items, while raising the tariff on electric vehicles from 27% to 102%. Several European countries are also preparing to raise tariffs on Chinese goods. With these restrictions and reduced market access, China is overproducing and turning to Asian and ASEAN markets, including Thailand, which still has purchasing power,” the FTI chief said.
“This scenario is forcing many Thai SMEs to shut down, while others, although still operational, have had to close production lines but have retained their sales or marketing divisions, shifting from manufacturing to import of goods for resale," Kriengkrai explained.
The impact of low-priced imported goods being dumped in the market has affected more than 20 out of 45 industrial groups within the FTI last year. If no effective measures are taken this year, it is expected that more than 30 industrial groups may be affected, he warned.
Kriengkrai also noted that most of Thailand's industries are still traditional and do not meet modern global trends. They often operate as original equipment manufacturers, producing similar products as those from neighbouring countries like Vietnam, Indonesia, and Malaysia. But Thailand faces disadvantages in terms of costs such as electricity, labour, and a shortage of production-supporting labour due to an aging population, leading to reliance on foreign labour, thus reducing competitiveness.
Labour-intensive industries, such as clothing and garments, have relocated to neighbouring countries where more labour is available.
Meanwhile, high-value and high-tech industries have not made significant investments in Thailand, with most of the investments going to Singapore or Malaysia. Currently, only a few FTI members – less than half – have managed to transition to higher value-added products, while the majority, primarily SMEs, have not been able to make this transition, he said.
He said all industrial sectors were at risk of further closures, because Thailand’s measures to protect domestic industries, compared to those in neighbouring countries like Indonesia, are not stringent enough or sufficient to slow the influx of low-priced and low-standard imported goods into Thailand, Kriengkrai added.
Foreign investors in Thailand are also affected. Recently, Suzuki Motor (Thailand) Co Ltd announced the closure of its production plant in Thailand by the end of 2025 due to declining sales and competition from Chinese EVs. Earlier, Tan Chong Subaru Automotive (Thailand) Co Ltd announced it would cease car production in Thailand by 2024 due to ongoing losses, affecting suppliers of parts and components for internal combustion engines, some of whom may also have to shut down.
Kriengkrai’s views are consistent with those of Wirote Rotewatanachai, director of the Iron and Steel Institute of Thailand, who revealed that as of April 2024, capacity utilisation of the Thai steel industry for the first four months of this year was about 29.3%, compared to 32.4% in the same period last year.
Wanchai Panomchai, secretary-general of the Thai Industrial Standards Institute (TISI), said that to protect Thai manufacturers from substandard and cheap Chinese imports, the TISI had been inspecting Chinese goods sold in markets and online, with the aim of eradicating low-quality products within six months. Urgent measures have been implemented, including the "3Rs" strategy – rapid inspection, rapid supervision, and rapid enforcement.
“We are increasing the frequency of inspections across various online platforms, and expanding these findings to identify storage locations and online advertising channels to address the issue comprehensively,” he said.
"From September 2023 to April 2024, the TISI seized non-standard Chinese goods worth over 76.2 million baht, representing 38% of the total value of 199.4 million baht. From September 2022 to April 2023, TISI seized non-standard goods worth 47.7 million baht, with Chinese products accounting for 13.8 million baht, or 29%, of the total," Wanchai concluded.
Asia News Network (ANN)/The Nation (Thailand)