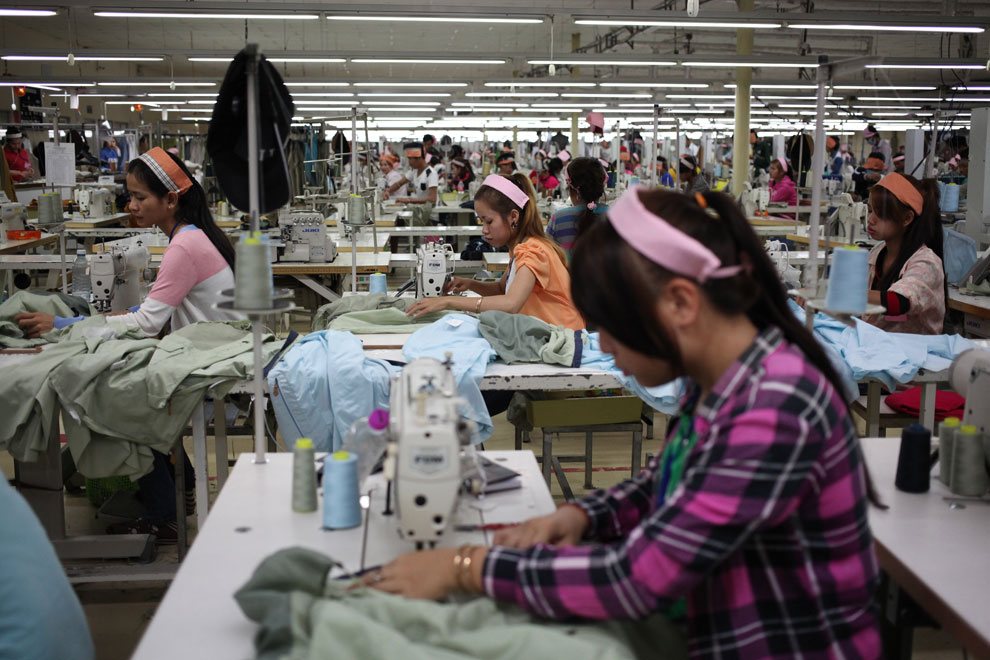
Garment workers in the sewing division of a factory in Phnom Penh. Hong Menea
Switch Garment, in collaboration with New Delhi-based The Energy and Resources Institute (Teri) and the Institute of Technology of Cambodia (ITC), kicked off a series of energy audits in Cambodian garment factories.
The audits are devised to identify the best cost-effective options to build a more economically-resilient industry that is able to meet purchase orders, while constraining its environmental footprint.
Switch Garment said in an August 24 statement that the audits will analyse the energy intensity of garment manufacturers’ facilities and identify opportunities for cost savings and production optimisation.
Under Switch Garment, the audits will serve to inform clean energy investment by factories and to identify factories’ training needs to strengthen sustainable energy practices, it said
“Faced with pressures from international buyers to reduce environmental footprints, 30 factories have signed up as partners in the Switch Garment programme to date, while 20 more will be recruited later this year,” it added.
Robert Hwang, managing director of PPSEC Co Ltd, said high electricity costs and growing sustainability requirements from buyers are significant challenges for factories in Cambodia. “We have joined the Switch Garment programme because good energy management is important to remain competitive in the market.”
Garment Manufacturers Association in Cambodia (GMAC) general manager Ly Tek Heng, who has been leading the engagement with factories on these audits, said: “International brands that buy from garment factories in Cambodia now focus heavily on sustainability due to growing environmental awareness of consumers and the sector must keep up with the trend to remain competitive.”
Launched on September 11, Switch Garment is a joint venture between the GMAC, the Seoul-headquartered treaty-based international organisation Global Green Growth Institute (GGGI) and French NGO Geres-Cambodia. The project is funded by the EU through the Switch-Asia programme.
According to Switch-Asia, GGGI’s economic modelling projects that a 20 per cent increase in energy efficiency in the garment sector would lead to a 31 per cent surge in energy productivity by 2030 and $2 billion saved in energy costs.
It said: “Cambodia’s garment industry is losing its edge compared to other countries like Bangladesh, Myanmar and Vietnam, given its high energy costs as well as recent increase in the monthly minimum wage, lagging infrastructure, productivity and logistics.
“The cost of electricity from the national grid in Cambodia is the highest in ASEAN. The average energy cost per tonne of garments is $560.
“Energy costs constitute a significant share of the total production costs, contributing 16.7 per cent, which is also higher than neighbouring countries.”