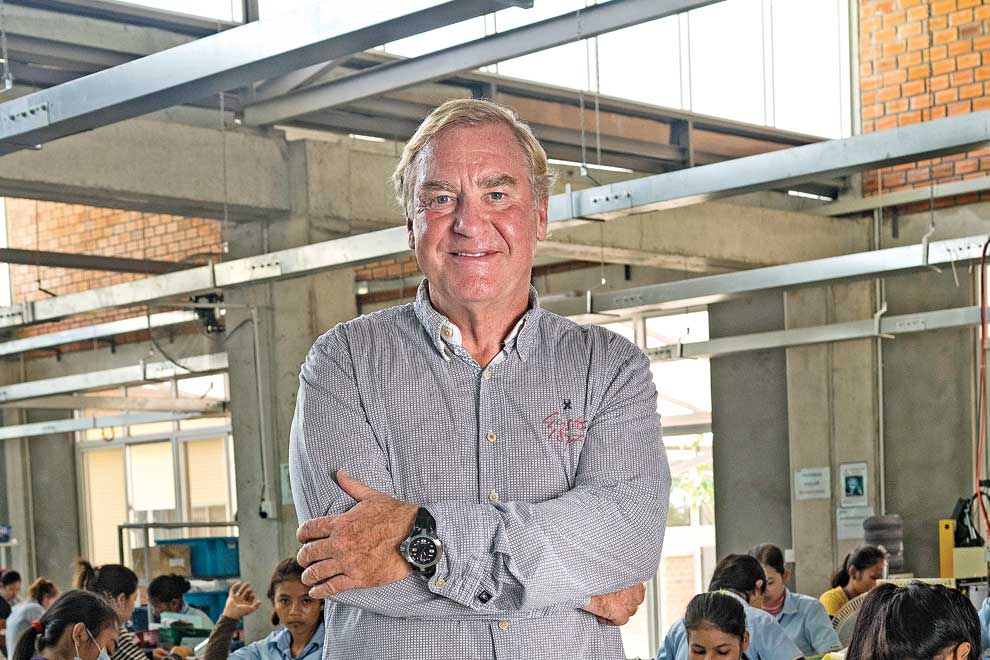
Piet Holten, president of Pactics Cambodia poses for a photo at Pactics Cambodia in Siem Reap province last year.
Cambodia’s garment industry was faced with the highly sensitive issue of wage-related strikes early last year, as well as criticism on the treatment of employees and poor work conditions. The Post’s Ananth Baliga sat down with Piet Holten, president of Pactics Cambodia, to discuss employee-friendly policies instituted by the company and environmental and sustainable practices used as part of its CSR initiative.
Why did Pactics decide to setup their operations in Cambodia?
The reason for that is I was already looking to add a second manufacturing location to the one we had in China. Prices in China rose and the US dollar to the RMB was shifting quite dramatically. So I thought it might not be sustainable to continue in China. But to start in a country [Cambodia] that you do not know is always a risky operation.
So I thought let’s start small and do it like an experiment. I drove around Phnom Penh to look at facilities there and I didn’t like what I was seeing with the garment factories. There are good companies there but I didn’t like the environment. So I went to Siem Reap and we looked around here.
We started with half a shop house and from there we grew from 15 people in a shop house to 30 people in a full shop and then move to our own facility. We also got help from the Dutch government to build this project that helped quiet a lot.
What kind of products are you manufacturing here?
We make cleaning cloths and bags made from microfiber. We do that for a number of large brands. We are not the cheapest in the world. So we cannot go for the lower end market. High end brands also have an appreciation of the corporate social responsibility (CSR) work we do.
The two biggest ones are 20 million cleaning cloths for Rayban and for Oakley we make 12 million bags. We have other brands like Bulgari, Prada, Versace, Armani, Tiffany and Ralph Lauren.
Your production line is similar to other garment factories but what differentiaties it from conventional factories in Cambodia?
We make a much simpler product than garments. So we can employee really unskilled labour. We have less polluting operations than garment factories do. When they do the washing, sanding and acid wash, for example, for jeans that is not very nice. We do screen printing here that has solvent in it but we do that in a separate room.
We have ventilation in there and take care of employee protection. The processes we use are very environment friendly. The way we set up this factory can also be done for other garment factory. And that comes from the way we want to treat our people.
You have many CSR activities and processes in place for your employees?
When you ask companies in the Western world about CSR they will almost entirely translate that to the environment or charity. We also do environment control here and have tried to build this factory as a green factory, but it has to do with how you treat your employees.
A happy employee makes good products. How can you be productive, for example, when you don’t eat well? Hence we have our own kitchen. We monitor their calorie intake – everybody takes in 80 grams of protein and 200 grams of vegetable.
We have the normal maternity leave but many workers didn’t come back after that because there was no one to take care of and feed their babies. So the day care centre is a relatively low cost way to get the mothers back and make sure the family still gets their income. Our sick leave is under 1 per cent and 15 per cent for employee turnover. In Phnom Penh they have high turnovers because they work with many migrant workers, like in China.
What are some of the green measures built into the factory?
When you have the chance to build something, build it so it fits this climate. So what we did is make smaller building because they are easier to cool. We centred them around the courtyard. That will cool the building around it.
The natural wind is south to north and the way the building is built we automatically get that air flow. This [north-south positioning] also makes it possible for us to run the factory without lights. Only during the monsoons do we need to switch on the lights. We recycle rain water that we use to flush the toilets. We have also installed solar panels on the bike parking. The expectation is that we can power 40 per cent of our usage with that.
We are not an NGO or social enterprise. We have to make money in a difficult market and with a very a low end product and what I want to prove is that it can be done.
Within the garment sector wages are a big issue. How does Pactics deal manage employee wages?
We compete on the same labour market as garment factories. What we did is a living wage study. We looked at what does a typical family that works here need as income to make a decent living. So, we provide lunch at a subsidised rate and we pay health insurance. Based on the study, a decent wage in Siem Reap is $125, with 10 per cent as savings.
We have two skill levels- level one are people who don’t operate equipment and level two operate machinery. So $125 is our guaranteed wage. Skill level one when they reach the target can make 15 per cent over the minimum and 30 per cent for level two. The target is determined by the average that the group makes for a particular product.
What are the future plans for Pactics?
We are scaling down our Chinese operations and we will probably have 400 people here by the end of this year. We currently make 45 million products here, including China’s production. I think China is seven million and 38 million in Cambodia. We are moving the remaining seven million here.
This article has been edited for length and clarity.
Contact PhnomPenh Post for full article
SR Digital Media Co., Ltd.'#41, Street 228, Sangkat Boeung Raing, Khan Daun Penh, Phnom Penh, Cambodia
Tel: +855 92 555 741
Email: [email protected]
Copyright © All rights reserved, The Phnom Penh Post