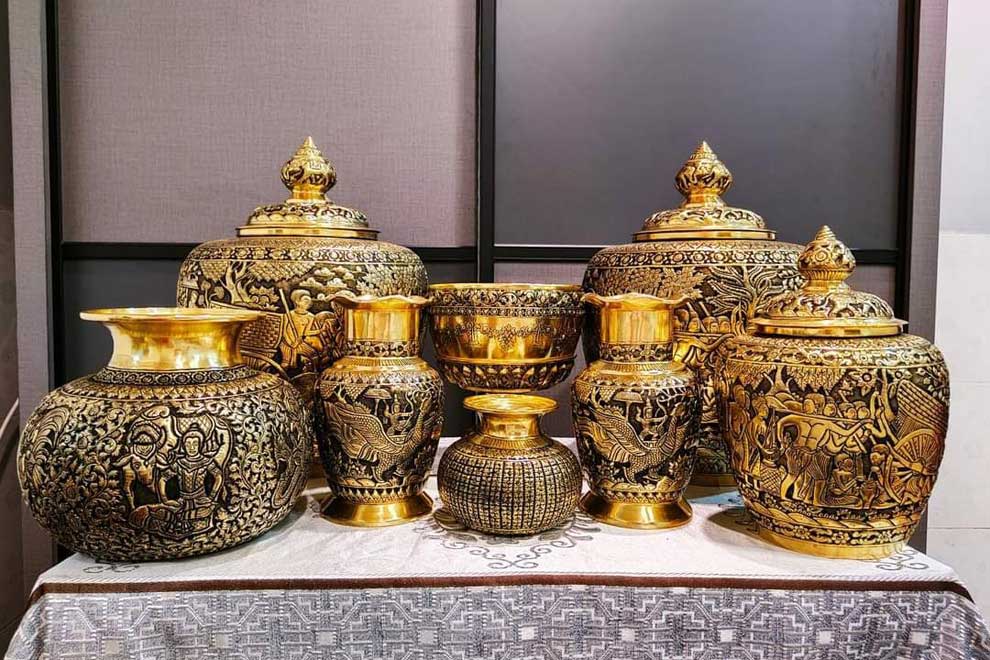
These elaborately carved vases can cost hundreds of dollars per kilogramme depending on thickness and detail. PHOTO SUPPLIED
Van Libo, now in his seventies, is from the second generation of his family to work as an engraver of copper and silver at the Phnhi Tes Handicraft Shop in Prek Kdam Muoy village of Koh Chen commune in Kandal province’s Ponhea Leu district.
Now, as he gets older, a third generation of his family have inherited the profession from him and six of his nine children are working with copper at the shop.
“Six of my siblings started copper engraving careers after being taught how to do it by our parents who inherited this knowledge from their family,” said Van Nila, 44, the eldest of the nine children.
The Phnhi Tes Handicraft Shop is being handed down to the 3rd generation and already has members of a 5th generation working at the shop with nieces and nephews of Libo carving, installing and polishing the items.
“From one generation to another, we have developed these items to suit the requirements of customer requests. But what we have still maintained is the tradition of producing these copper engravings in stages using the same methods,” she said.
Among the people in Koh Chen commune, only residents of Koh Chen village and Prek Kdam village make copper and silver engravings. They have always conducted this business going all the way back to ancestral times.
Koh Chen commune chief Nhem Soeun said that over 75 per cent of the residents representing more than 100 families in Koh Chen and Prek Kdam villages make copper and silver engravings.
“Koh Chen and Prek Kdam consist of people who have been doing engraving for a long time, well before the Pol Pot era and even before the Sangkum Reastr Niyum era,” he said.
Nila grew up seeing her father Libo working as an engraver. She said that although the engraving work was handed down, it was necessary for people to study the process in-depth in order to get it right.
She added that carving has many stages and certain carvings walked forward or backwards, but certain people make engravings without rules, so they did not look beautiful.
At present, Phnhi Tes Handicraft Shop is focused on producing bowls, vases, jars and boxes by hand.
Van Sitha, 30, is the seventh son to learn the art of engraving from his father and he is more capable than any other student in the art of carving decoration into copper.
He said that there were not as many families now who maintained the work of ancient handicrafts.
He added that the hand-made copper engravings required 100 per cent pure copper and the pieces go through several laborious stages.
A copper plate is cut and then heated two or three times before the object is coated with resin for carving and the production of each object requires three to four people.
“The first stage is prepares the object. The second stage is carving the relief. The third stage fixes the carving and the last stage is the cleaning. Customers need polished sculptures. The shop added this last stage to suit the requirements of the clients,” he continued.
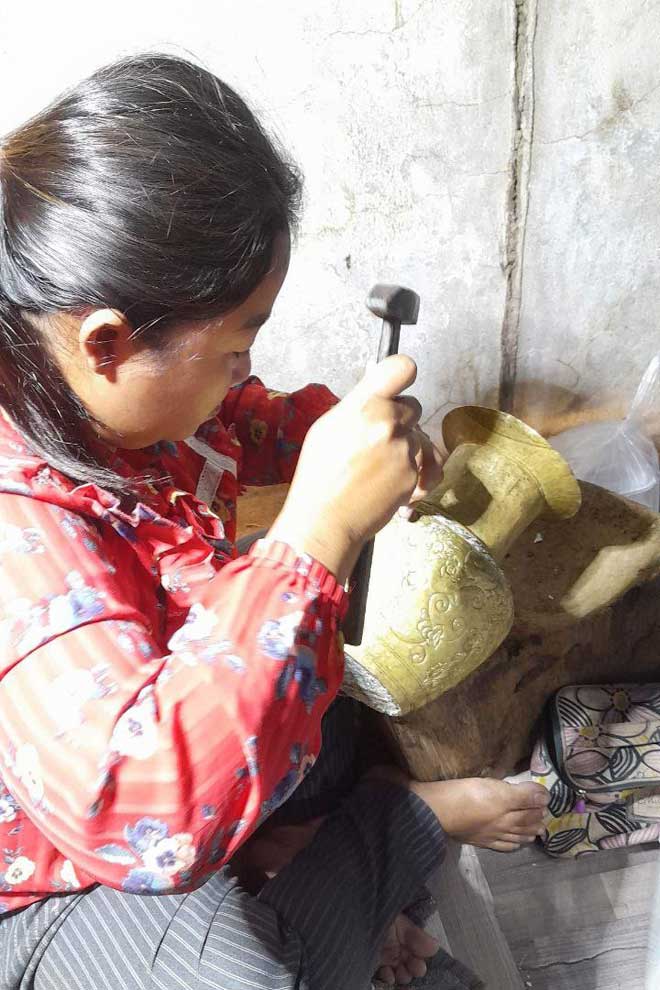
An artisan engraves a copper and silver vase at Phnhi Tes Handicraft Shop in Prek Kdam Muoy village in northern Kandal province’s Ponhea Leu district. PHOTO SUPPLIED
Nila, who is also in charge of communication and design, said that the bowls and the vases were popular with customers for home decoration and for use at special events.
She added that some clients who can afford it order a set to display in their homes. It is easy for them to have a housewarming party if they don’t have to hire a decorator and it can take the shop up to a month.
“For example, when a guest orders a pair of bowls we make a dozen of them because it is more cost effective. When we know that the objects sell well, we are not afraid to make more,”she stated.
The shop is focused on the use of decorative styles on these objects and for good handicraft products they charge $100 to $200 per kg, depending on the details of the engraving.
She said that, in general, a 25cm bowl uses 4kg of copper and a pair of vases 32cm tall weigh 2.7kg each.
“These are for my creations. For some other products, they are carved shallow and the copper is thinner if they are less well-off customers. When the copper is thick and the workdone meticulously they can keep it for 100 years and it won’t rust or wear out,” she added.
However, they have also been faced with some problems when customers question why the copper changes colour.
“We find it difficult to explain this to customers, some of whom don’t have a clear understanding of metals. But copper sculptures can be restored to be as beautiful as they were originally, so it is easier than foreign goods. Obviously, when porcelain glass is broken, we cannot repair it. But our Khmer copper can be restored or repaired to be like before,” she continued.
Sitha, a new worker at Phnhi Tes Handicraft, said that the unique quality of these copper engravings isthe detail present in the carving of the relief because casting cannot compete with carving.
“If anyone in the country could do this like us, they would do it like us and there would be no need to buy from us to resell. From the beginning, when I grew up, my mother delivered goods to sell in O’Chrou district of Banteay Meanchey province or Poipet and Thai traders would hire us to carve,” he said.
“I would like to tell our Cambodian people who understand to help spread the word so that our Cambodian items will not be lost. Foreigners have been collecting and buying the items for a long time and they could say the items belong to them,” he continued.
Through cooperation between the Ministry of Commerce and the Ministry of Tourism, Koh Chen village is now being promoted to tourists.
Koh Chen commune chief Nhem Soeun said that prior to the Covid-19 pandemic, the Koh Chen community received a lot of tourists, but now the number of visitors to the handicraft shop remained low.
Long Bonna Sirivath, spokesman of the Ministry of Culture and Fine Arts said that the ministry has inscribed these types of engrave products in the “List of National Intangible Cultural Heritage in 2004.