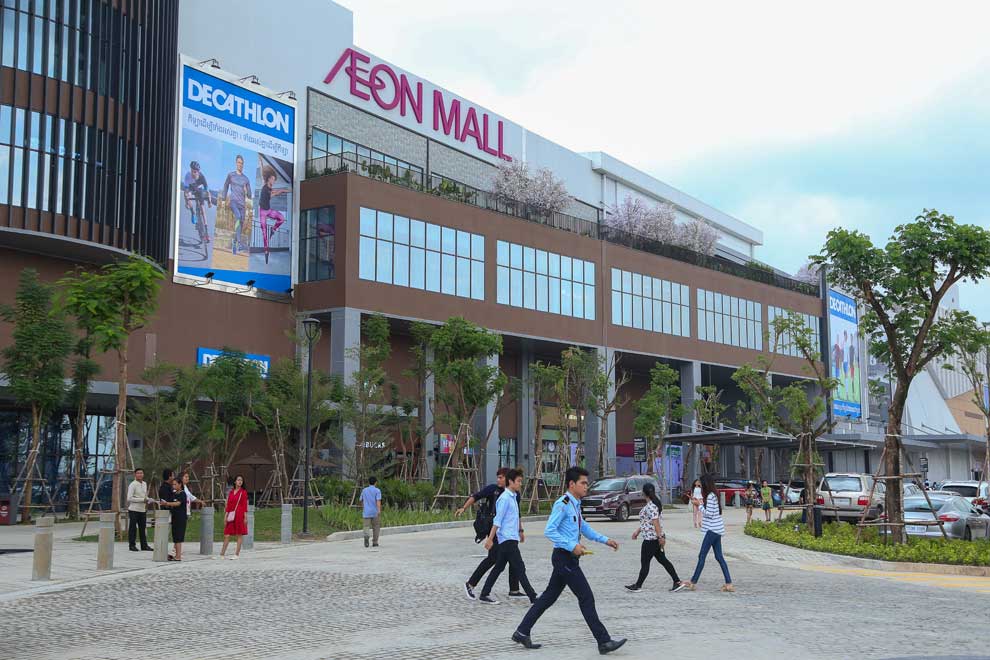
AEON is one of only two major Japanese companies that have chosen to invest in Cambodia. Addressing investors’ concerns may help increase Cambodia’s chances to welcome the next batch of Japanese companies. Hong Menea
Fine-tuning “industrial connectivity” is not new to Japan, which has a strong production and supply chain in the Southeast Asian region.
Japan has strategised the way it does business in the region by considering the latter as a single integrated production site with multiple exporting markets at the same time.
Integrated production site refers to the approach that Japanese companies diversify its production lines in various ASEAN member states following comparative advantages and incentives that each country has to offer.
For instance, the upper stream of works that require higher-skills can be located in countries with more skilled labour forces, while the lower stream can be outsourced to other neighbouring countries with non-skilled or lower-skilled labour, with much lower wages.
This has been made possible thanks to the enhanced connectivity in the region and this is where the concept of “industrial connectivity” is derived from.
Other than benefitting from a combination of comparative advantages, industrial connectivity is also important for diversifying risks.
For instance, there were compelling reasons for Japanese companies to spread their production lines to various countries when anti-Japanese sentiment was heated up in China, coupled with the disastrous flood in Thailand in the early 2010s.
The trend of factories shifting out is what we now know as the Plus One effect such as “China+1” and “Thailand+1”.
During that period, Myanmar was the “darling” of the next frontier market for Japanese investment. Cambodia was not a major destination but there were companies like Minebea and AEON who chose Cambodia.
Minebea’s case is the real successful example of “Thailand+1” in which the company can enjoy benefits from both Thailand and Cambodia’s connectivity and incentives while averting risks.
This was the major wave of Japanese investment in Cambodia that assisted the latter to diversify its industrial base beyond the garment sector.
Japanese companies are well known for their good treatment of workers, providing uniforms, air-conditioned factories, dormitories, and even opportunities for informal education.
Strikes against Japanese companies are things that we have never heard of. The most important thing is these companies prosper too.
With the current Covid-19 pandemic, the US-China trade war and superpower rivalry, another wave of Japanese factories’ outflow from China is occurring.
ASEAN member states are vying to welcome those factories, but this time Vietnam is the “darling” destination owing to geopolitical reasons, large market, investment-friendly climate and skilled labour force.
Supply chain diversification
Japan’s Ministry of Economy, Trade and Industry (METI) and the Japan External Trade Organisation (Jetro) are the leading implementors for the so-called “Overseas Supply Chain Diversification Support Project”.
This seeks to enhance Japan’s supply chain resilience in Asia, especially through bolstering ASEAN-Japan economic and industrial cooperation.
The project can provide a subsidy of up to approximately $50 million for Japanese companies seeking to increase the production capacity in ASEAN member states. In mid-July, the first batch comprising of 30 companies were selected out of the 124 applicants.
In the breakdown, while some companies have multiple destinations, Vietnam received the most number with 15 companies, followed by Thailand (six), Malaysia (four), Philippines (three), Laos (two), and Myanmar and Indonesia one each.
Product-wise, factories bound for Thailand are more advanced, producing rare metals, car spare parts, vaccines and semi-conductors.
For Vietnam, there are varieties of products ranging from personal protective equipment (PPE), air-conditioner motors, smartphone parts, hard-disk drive, car spare parts, and rare earth magnets to semi-conductors.
For Myanmar and Laos, products comprise of medical gowns, gloves and hard-disk drives.
If one specifically focuses on the Mekong region, Cambodia is the only country that was omitted from this new wave of Japanese factories’ outflow.
Many reasons can be speculated, such as geopolitical considerations, connectivity to the region, investment climate, weak infrastructure, among others.
In October last year, the chief representative of Jetro-Cambodia, Miyao Masahiro, offered a gloomy picture of Cambodia’s investment climate.
From the Japanese investors’ perspective, especially manufacturers, electricity shortage, stability and price are still posing challenges for Cambodia if compared to Thailand and Vietnam.
Another challenge is the taxation system which is still different from the surrounding countries. Trade customs system, trade-related procedures, logistic system and cost are also major obstacles for investors seeking to enter Cambodia.
He was not hopeful for Cambodia to attract large companies as he thinks currently, the Kingdom is only fit for Japanese SMEs.
Such observations are rather discouraging for Cambodia-Japan relations which are seeking more enhanced economic interactions when aid is gradually decreasing.
Probably, Cambodian and Japanese policy-makers need to work out more for favourable and practical solutions for mutual benefits, friendship and strategic partnership.
Addressing investors’ concerns may help increase Cambodia’s chances to welcome the next batch of Japanese companies to be selected by METI and Jetro.
Indeed, countries are struggling to invite investors amid this global economic slowdown, and it is conventional wisdom that it generally takes time and perseverance to convince Japanese companies to come, but when they do come, they are here to stay.
Equally important, they stay to prosper together with local people.
Sim Vireak is the strategic adviser to the Asian Vision Institute