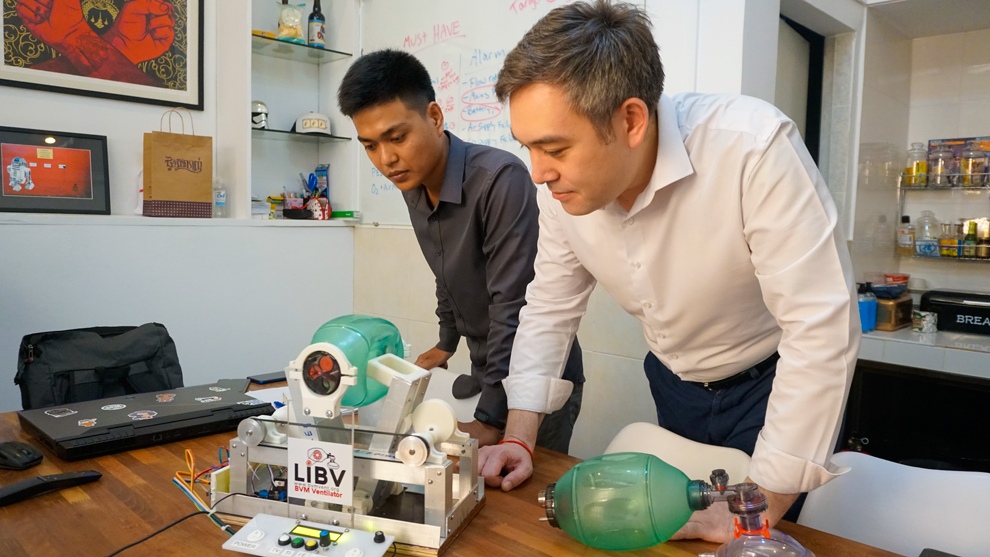
Allen Dodgson Tan (right), director of applied technology at the Golden West Humanitarian Foundation, showcases the prototype for the ventilator alongside chief designer Theara Kong. Post staff
As FORD, General Motors and even Formula 1 teams turn their expertise towards making ventilators during the current Covid-19 outbreak, a group of Cambodian engineers is also leading the charge.
Allen Dodgson Tan, the director of applied technology at the Golden West Humanitarian Foundation (GWHF), told The Post that its Design Lab is currently using 3D printers to make face shields for medical workers and testing a prototype of a low-cost ventilator for those infected.
Manufactured at a cost of only $100 per unit, the Low-Resource Improvised BVM Ventilator (LIBV) is currently in the testing stage, with the aim “to address a shortage of ventilators worldwide and specifically in Cambodia”, said Tan.
Engineer Theara Kong, 24, and a coalition from the US and the Kingdom – including Cushbots Corporation (US), J-Hook Co Ltd (Cambodia) and professors from Pennsylvania’s Villanova University – have designed the LIBV.
It took six days for the device to go from an idea to the prototype stage, Tan said, which would not have been possible without the use of 3D printers.
“We hope we can start manufacturing them within weeks. We also hope our design will be useful for other developing countries which have limited resources,” said Tan.
US Ambassador to Cambodia Patrick Murphy, who visited the facilities last week, said he was “proud to see Americans and US organisations play a role to help Cambodia stop the spread of Covid-19”.
He added that the effort was indicative of “longstanding partnerships [between] US government health agencies and Cambodian counterparts [who] are giving back to the Kingdom and working together”.
The GWHF Design Lab, established in 2013, houses the Kingdom’s largest 3D printer, which with it being a “consumer-level device,” is symbolic of making the most out humble resources.
The foundation was an Innovation Awards Honoree under the “Tech for a Better World” category at the 2016 Consumer Electronics Show in Las Vegas for its Advanced Ordnance Teaching Materials (AOTM) programme.
The AOTM initiative is dedicated to creating 3D-printed replicas of UXO for the training of deminers.
However, to address the outbreak, eight engineers, divided into groups of four, are working round the clock to build face shields.
They are producing 50 face shields per day and aim to make 3,000.
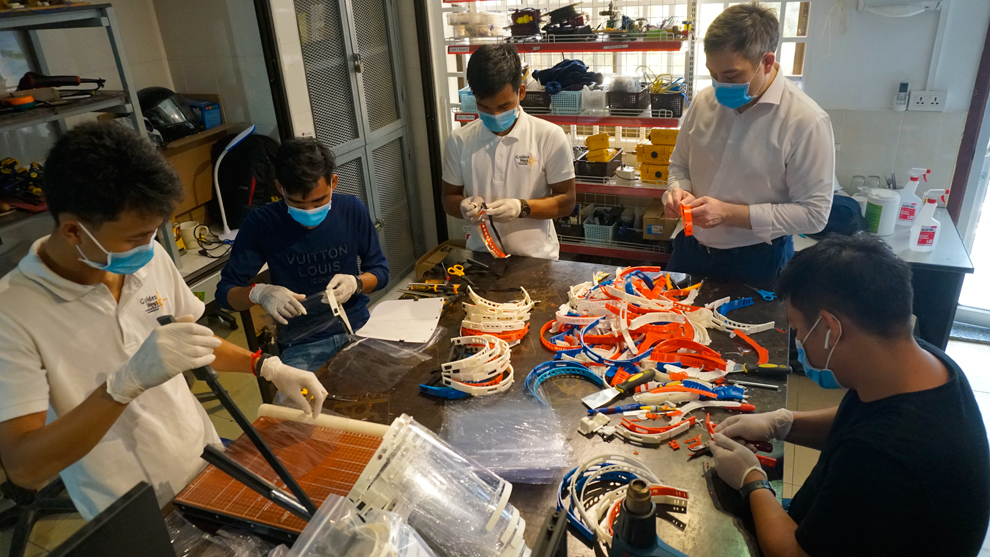
Eight engineers are working around the clock to fabricate face shields for medical workers. Post staff
“The ‘lads’ have volunteered to work in shifts to cover 24/7 production. This is an amazing commitment from the engineers.
“The face shields cost $3 [per unit] to manufacture, including manpower, materials and machine time. This does not include management overheads or rental of the facility,” Tan said.
While GWHF is covering the cost of the labour, the Cambodian Health Professionals Association of America is funding the materials.
Tan, who is also the president of the board of the American Chamber of Commerce in Cambodia, stressed that the medical equipment will only be used as part of the Kingdom’s efforts to combat the outbreak.
“There have been multiple commercial entities and individuals who have looked to purchase these face shields from us for use in their private business or for exporting to other countries. We denied them all immediately. Cambodia cannot afford to lose any medical equipment,” the Cambodian-American stressed.
The face shields, modified versions of a Czech open-source variant by Prusa3D, have been adapted to accommodate Cambodia’s manufacturing capacity.
Rather than using laser cutters to puncture the hole for the elastic, the Cambodian engineers have devised a way to use paper cutters and punches to keep costs down.
Mork Tongly, 25, was among the group of engineers working when The Post visited the facilities.
“These printers are very small, but they let us make the face shields uniformly. I’m proud to work and help my country right now using technology,” said Tongly.
Tan said GWHF aims to produce the ventilators, alongside the face shields within the next few weeks.
“3D printing allows us to make very professional products. Many DIY [do-it-yourself] homemade visors have a limit to comfort and durability, which is different from what we do can with professional fabrication techniques.
“This project highlights how the Fourth Industrial Revolution can empower communities to solve their own problems.
“The localisation of production is important for national security, and we are honoured to be able to contribute to the Kingdom even in a small way,” said Tan.